What is the Wear Life of Electrical PPE?
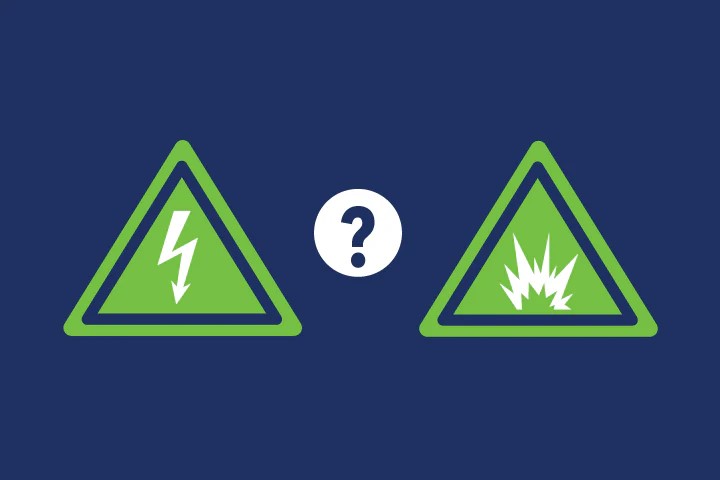
The Safety Question
More often than not, the motivation behind the question is related to how long the products will retain the protectiveness/safety qualities over time and repeated washings. Another question often asked is if there are any standards that require periodic retesting or whether the products have an expiration date. This is an excellent question, and the answer varies significantly for electric shock as compared to arc flash.
The Electrical Shock Hazard
The voltage rated rubber insulating gloves are covered by the ASTM D120 standard (Standard Specification for Rubber Insulating Gloves). This standard requires new gloves to be tested and put into service within 12 months of the initial test date. Once in use, the rubber voltage rated gloves must be retested every 6 months and, if they pass, the gloves are stamped with the new test date or expiration date and put back into service for another 6 months. This process is repeated until failure. Although it’s difficult to predict how many cycles the gloves will last, higher class gloves (class 2, 3 and 4) are thicker, so they tend to last longer than class 00 and class 0 gloves. If the gloves fail either the visual inspection or after physical testing in the dielectric glove testing machine, they are defaced to ensure no future use (typically a finger is cut off).
In addition, leather protector gloves should be over the rubber voltage rated gloves to help protect them from damage in use. The individual user is also required to inspect the rubber gloves before each use. There are a few methods that can be used, and employees should be fully trained on how to properly administer this inspection. Typically, the leather protector gloves are removed from service from contamination or wear.
The Arc Flash Hazard
Arc flash is a different story as there are no ongoing fabric or apparel tests required, beyond the important initial requirements (i.e. ASTM F1506 and F1959 etc.). Arc and flame tests can be performed on representative samples, but these tests are destructive. The care and maintenance of the garments should follow the manufacturers recommendations and, if a garment is damaged or shows significant signs of wear, it should be immediately removed from service so it can be repaired or replaced. This is often a judgement call and there is currently no expiration date for arc flash apparel.
Most electrical safety experts and safety professionals agree that it’s practical to set up a plan to replace arc flash suits/kits every 5 years or sooner. Shields and hard hats/liners should be replaced according to the manufacturer’s recommendations. This timeline can be reduced significantly depending on the level of wear and tear in use and the number of times it’s washed and worn. As an example, a customer in the utility industry that issues each employee one set of 40 CAL garments that are washed and worn daily, sometimes for hours at a time. These garments will undoubtedly have to be replaced well within the 5-year timeline. Other electrical contracting customers typically wear their suits for 10-15 minutes a few times a week to verify that the equipment they’re working on is properly de-energized. In these cases, the garments routinely remain in service for approximately 5 years.
It’s commonly known that arc rated fabrics can lose some strength over time. The amount of strength loss varies by fiber type and it can be impacted by environmental factors such as high heat and humidity and exposure to UV light etc. There is a 10-year replacement rule in place for firefighter turnout gear largely because of this concern. The same type of flame-resistant fabrics are often used to make arc flash suits. It would be very difficult, if not impossible, to predict exactly how much of an impact fabric strength loss would have on the arc flash protection, but it’s reasonable to expect a reduction beyond 5 years.
Time will tell whether any of the standard setting committees will discuss the possibility of including an expiration date for arc flash apparel. In the meantime, it’s a good practice for companies to plan on a 5-year replacement cycle and start to swap out arc flash apparel that is currently 5 years or older with new suits.
The Financial Question
The motivation behind the “what is the wear life of electrical PPE” question could simply be dollars and cents. While safety is paramount, it’s also important for companies to understand how long the garments will last so they can calculate the cost per use and build it in to their budgeting decisions. This is a critical question to answer because it may influence the amount companies are willing to invest upfront. If the electrical PPE is expected to last up to 5-years, you may opt for premium products that may cost more upfront, but they’ll be a relative bargain over the 5 years when you consider the many advantages they bring to the table.
The technology of arc flash apparel has improved dramatically and some of the new premium products address the many complaints safety professionals have heard from electricians that push back on wearing electrical PPE. By offering a higher level of comfort, increased mobility and better visibility, safety professionals can send a positive message to their workers that can increase the likelihood that they will wear it when required. This will help keep them safe and help the company stay in compliance.
The Enespro PPE Solution
The team at Enespro PPE has been involved in electrical safety products for decades. Their goal in launching Enespro PPE was to reinvent the electrical PPE category by introducing USA made products with new features that help solve problems with traditional electrical PPE. The innovations in their line of arc flash PPE were gathered from meeting with hundreds of safety professionals and electricians. The majority of their feedback was focused on improving comfort, mobility and visibility so their new line includes:
- AirLite™ is the lightest weight line of 8, 12 and 40 cal kits on the market
- ActiveCool™ underarm venting has 5x’s more stretch and 3x’s more airflow
- OptiShield™ clear-grey face shields dramatically reduce color distortion
- 40 CAL Vented Lift-Front Hood option with rear cooling fan now available
- 12 CAL Shrouded face shield eliminates the need for uncomfortable balaclavas
- Custom PPE storage bag to protect face shields from damage